Automated Zinc Ash Removal in the Hot-Dip Galvanization Process
Workers in the hot-dip galvanization industry are exposed to high safety and health risks during the galvanizing process, especially when they are removing zinc ash manually. The use of automation in the galvanizing process to minimize such risks was studied and tested on a real-world galvanizing furnace in industrial use in a joint research project of the Berufsgenossenschaft Holz und Metall (BGHM, German Social Accident Insurance Institution for the Woodworking and Metalworking Industries), Fraunhofer IFF and IEHK Steel Institute at RWTH Aachen University.
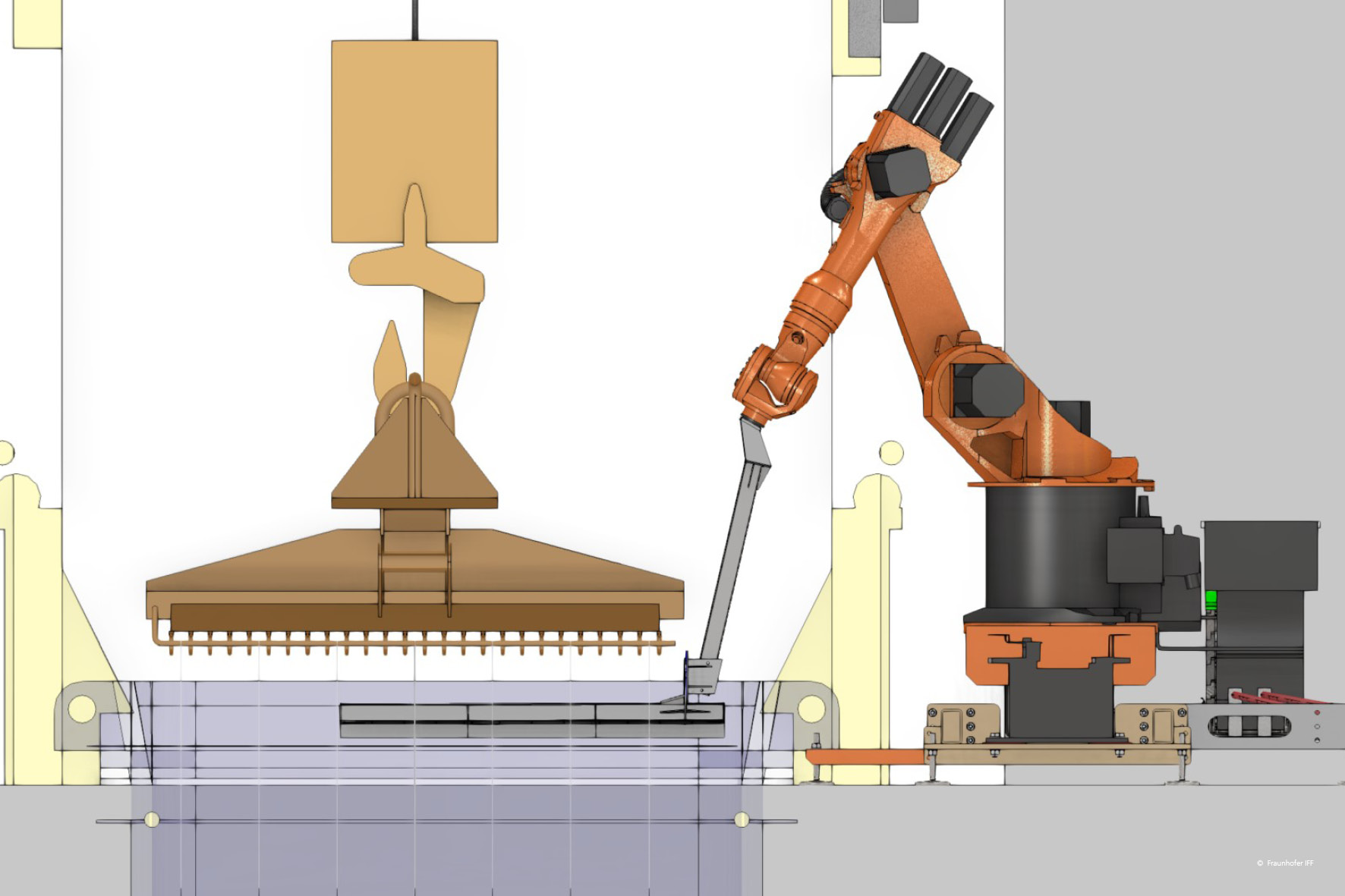
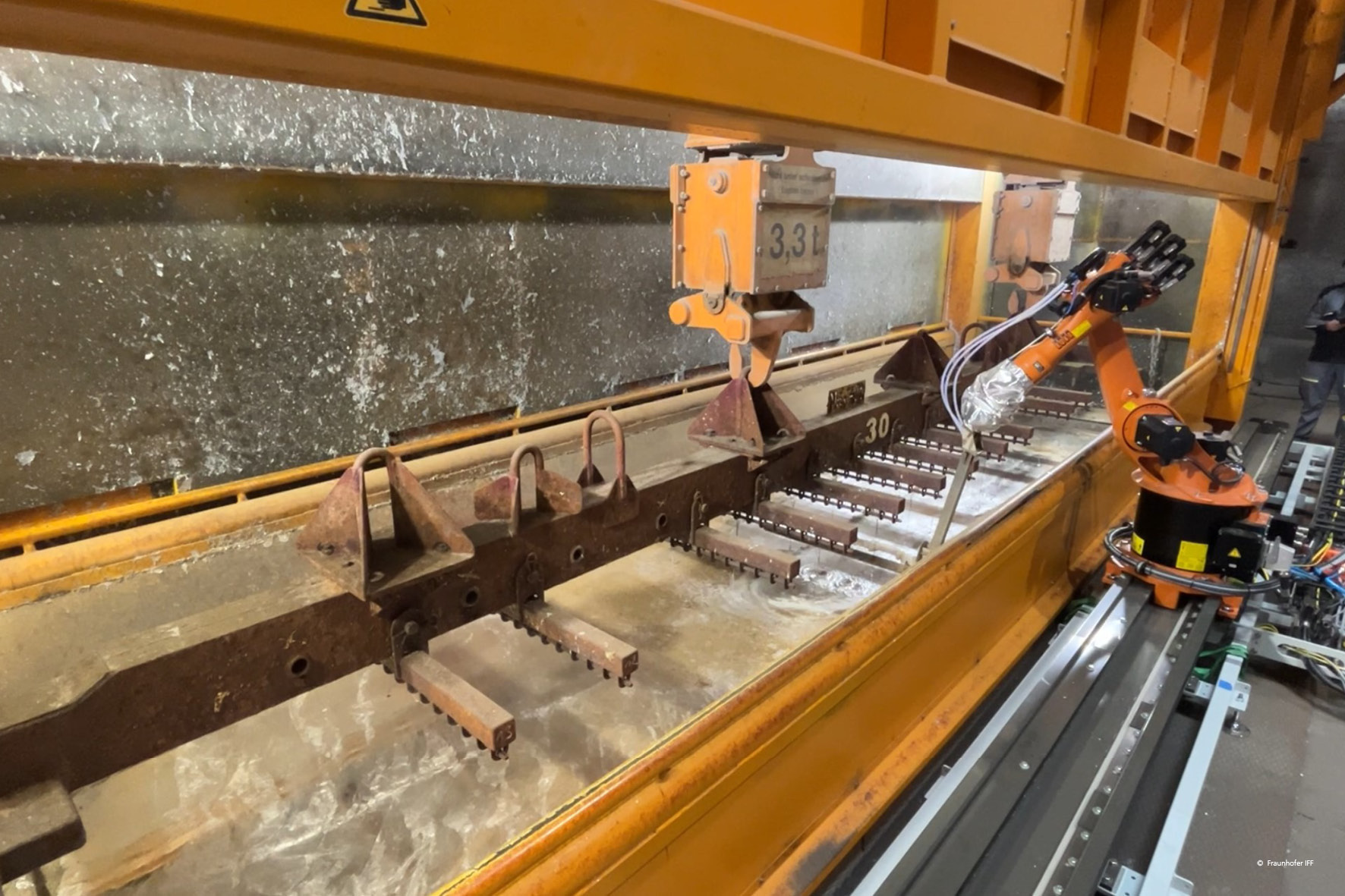
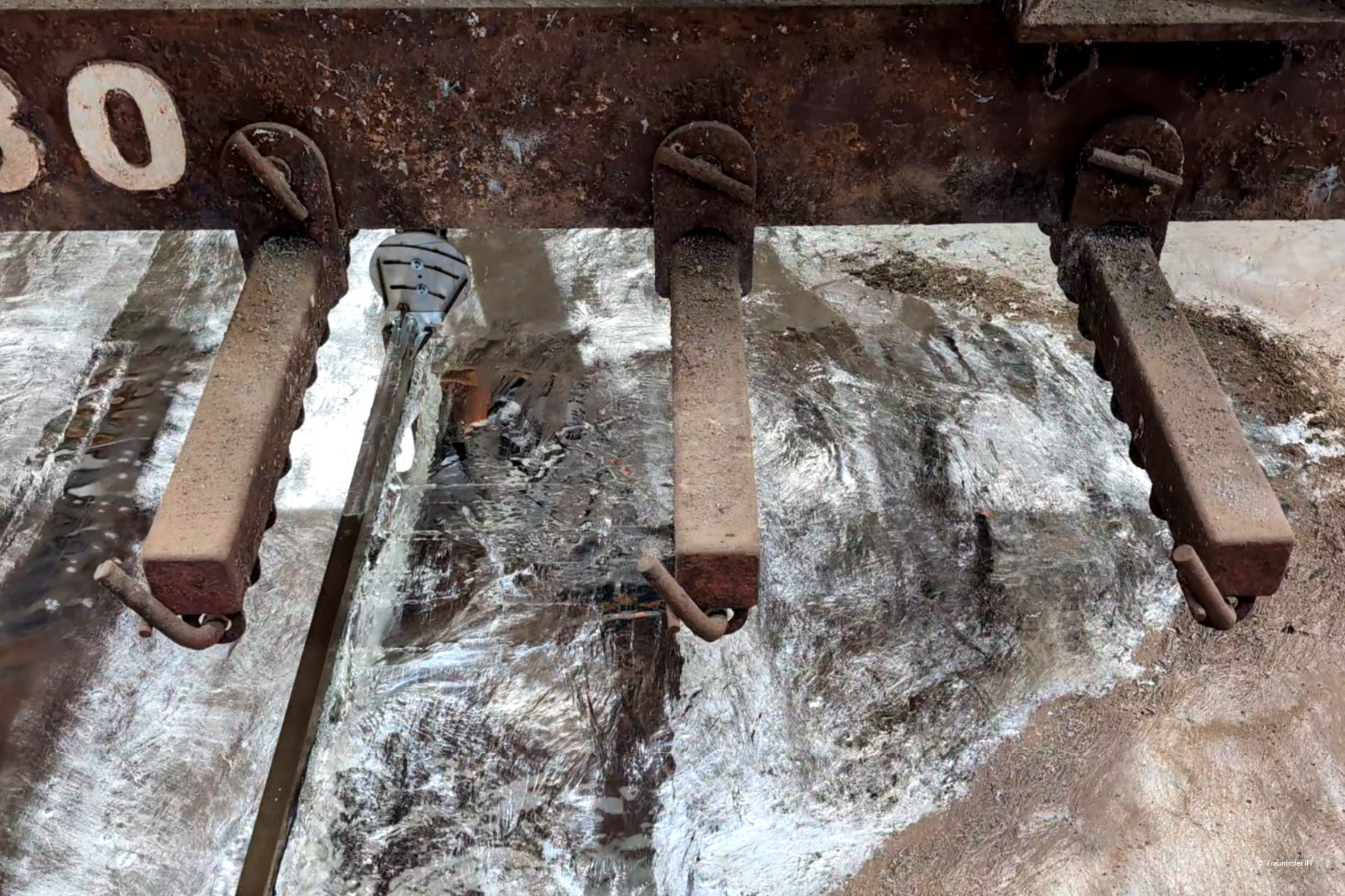
In hot-dip galvanizing, pretreated items for galvanizing, attached to a lifting beam, are submerged in a galvanizing vat with molten zinc, approximately 450° C hot. During the roughly ten minutes the process lasts, zinc, air and flux react with each other, producing various products. These deposit on the surface of the zinc bath and affect the quality of the zinc coating of the galvanized items lifted out of the melt adversely.
The main focus is on zinc ash, which is produced by the vaporization of flux and deposits on the molten zinc. This ash must be removed manually as part of the overall process. Galvanizing furnace operators use a mechanical skimmer to push the zinc ash from the surface to the front of the galvanizing vat. These employees are exposed to several risks in this process, such as the danger of falling into the molten zinc. Inhalation of fumes poses additional risks. “The inhalation of hazardous substances from the rising zinc fumes is a serious health hazard for employees,” stresses Dr. Andreas Vossberg from the Berufsgenossenschaft Holz und Metall (BGHM). Automating zinc ash removal could lower these risks significantly while reducing the staff required at the industrial galvanizing vats.
The Berufsgenossenschaft Holz und Metall (BGHM), Fraunhofer IFF and IEHK Steel Institute at RWTH Aachen are addressing this issue in a joint research project that builds upon a successfully concluded feasibility study. The results obtained at laboratory scale will be transferred to industrial use.
The automated process is geared toward the manual operations typical in the hot-dip galvanization industry, which employees have to perform when removing zinc ash. The removal tool is mounted on a six-axis industrial robot that can be moved along the galvanizing furnace on a linear axis. This tool is then placed and moved in the space between the workpiece holders inside the galvanizing furnace, pushing aside the zinc ash on the surface of the molten zinc. Fully automating and using this process in a real-world environment is the objective of the project. “Using a robot enables more precise and safer operation, especially in areas in which human actions could be dangerous,” explains Torsten Felsch from Fraunhofer IFF.
In a first step, removal tools suitable for the industrial vat were designed and engineered. A gas-based removal system (jet boom) and a mechanical removal tool (skimmer) were supposed to be used. The following criteria were drawn up as guidelines:
- Weight: The removal tool’s maximum weight is contingent on the robot used, i.e., maximum load torque in the robot joints (especially at the flange between the removal tools and the robot hand).
- Dimensions: Tools must be modified for the galvanizing vat.
- Heat resistance: Materials must withstand temperatures as high as 450 °C.
- Stability and rigidity: Requirements are high because of the zinc’s density.
- Modularity: Tools ought to be modularized to facilitate repairs.
Preliminary functional tests and theoretical calculations were both performed with the removal tools engineered. A 1:1 scale wooden model of the galvanizing furnace, in which water and plastic particles were used to ascertain process parameters relevant to later use at the industrial galvanizing furnace, was used at the Fraunhofer IFF technology center first. These preliminary tests yielded valuable findings that helped maximize the efficiency of automated removal.
Then the defined removal tests were performed at the industrial galvanizing furnace based on the parameters of the preliminary tests. To do this, the entire robot system, including the linear axis, was transported to an industry partner (hot-dip galvanizer) and installed in front of the galvanizing vat. Zinc ash produced during other galvanizing processes was applied to the molten zinc by hand to obtain reproducible test results. Both removal tools—the jet boom and the skimmer—were used for the removal processes.
The zinc ash could be removed completely when the skimmer was used as the mechanical removal tool. “We were not only able to remove zinc ash effectively, but also the zinc oxide surface formed by the oxidation of molten zinc under ambient air,” explains Felix Oppermann from RWTH Aachen University. The skimming motion profile comprised initially slow skimmer movement over the surface of the zinc, followed by a pulsating skimming motion at speeds as high as 2 m/s during which zinc ash could be removed even in zones that could not be reached physically with the skimmer. There was never any collision with the suspension system.
The gas-based removal process, on the other hand, uses gas to move the zinc ash. “The gas flow rate plays a crucial role in the efficiency of the process. We had to ensure that the compressed air supply was optimal to achieve the best results,” says Gunnar Strauss from the Fraunhofer IFF. As expected, the surface of the zinc oxidized less in additional tests with nitrogen as the process gas than with compressed air.
The technical feasibility of the mechanical and the gas-based removal systems analyzed was successfully confirmed at industrial scale.
Particularly good results were achieved with the mechanical removal system, i.e., the skimmer. The speed at which it removed zinc ash was significantly higher as well. Good results were also obtained with the gas-based system, albeit the gas pressure and flow rate could still be optimized.
The research project demonstrated that the zinc ash removal process can be automated with robotics, even at industrial scale. In addition to a significant gain in efficiency, the important objective of lowering employees’ health risks was achieved in the project as well.
Closer human-robot collaboration is conceivable in another step. This can make even greater flexibilities possible in the process, among other things, when lifting out galvanized items. Dr. Andreas Vossberg from the BGHM stresses, “Automating the galvanizing process can not only increase employee safety but also enable substantial gains in efficiency in the production process.”